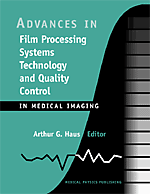
Advances in Film Processing Systems Technology and Quality Control in Medical Imaging
Author: Arthur G. HausISBN: 9781930524019
Published: 2001 | 245 pp. | Hardcover
OUT OF PRINT
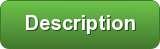
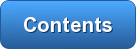
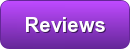
Description
Index: Glossary: Extensively IllustratedChapter Abstracts
Chapter 1
Film Processing Systems Considerations:
History, Image Quality, and Radiation Dose
Arthur G. Haus
Delaware, Ohio
Before the introduction and routine use of automatic film processing in radiology and medical imaging, medical x-ray films had to be hand processed. The first prototype automatic x-ray film processor was introduced in 1942. The first commercially available model could process 120 films per hour by using special film hangers, and the total time for processing one film was approximately 40 minutes. A significant improvement in automatic x-ray film processing was made in 1956 when the first roller transport processor for processing medical radiographs was introduced. This processor produced processed radiographs in approximately 6 minutes and accommodated all medical x-ray films designed for exposure with intensifying screens. In 1965, 90-second rapid processing was introduced. This advancement tailored new chemistry and new emulsions, and increased development temperature to 95 degrees F. In 1987, an automatic film processor was introduced which has a processing cycle of approximately 45 seconds: this processor requires special films. In 1990, an automatic film processor with an approximate 30-second processing cycle was introduced: this processor also requires special films and chemicals.
The choice of a screen-film combination, combined with film-processing conditions, substantially affects radiographic image quality (contrast, blur, and noise) and radiation dose. Film type (single-or double-emulsion, silver halide content, grain morphology, and spectral sensitivity), processing conditions (chemicals, temperature, time, and agitation), fog level (storage, safelight, light leaks), and optical density level affect film contrast. Film contrast characteristics (gradient) determine how the xray intensity pattern will be related to the optical density pattern in the radiograph. Light diffusion (spreading of the light by the intensifying screen), causes blurring. Factors involved include: the type of screen (phosphor layer thickness, light absorbing dyes and pigments, and phosphor particle size), and screen-film contact. The type of screen (phosphor layer thickness, light-absorbing dyes and pigments, phosphor particle size), speed of the screen-film processing system (sensitivity), film granularity, screen uniformity, and film contrast affect radiographic noise. Screen type, film type, processing conditions, and optical density level affect radiation dose.
Chapter 2
Results of Nationwide Evaluation of X-ray Trends (NEXT) Surveys and Mammography Quality Standards Act (MQSA) Inspections
Orhan H. Suleiman M.S., Ph.D. FAAPM
Center for Devices and Radiological Health - FDA
Rockville, MD
The quality of film processing has improved significantly over the past few decades because of ongoing educational efforts, laws, and regulation. This chapter focuses on technical measures of performance related to film processing, such as processing speed, darkroom fog levels, and radiation dose: and how these measures of performance vary in different clinical environments. These environments include U.S. mammography facilities before and after passage of the federal Mammography Quality Standards Act (MQSA) of 1992, mammography in Canada: facilities conducting chest radiography, lumbo sacral spine radiography, hospitals, private offices, and dental facilities.
Chapter 3
Accreditation Issues and Quality Control Tests Relating to Film
Processing
Priscilla F. Butler, M.S.
American College of Radiology
The American College of Radiology introduced their first imaging modality-specific accreditation program in 1987: the Mammography Accreditation Program. The primary goal of this program was to improve the early diagnosis of breast cancer (and, therefore, patient care) by setting standards for the performance of mammography and granting accreditation to those facilities that could demonstrate that they meet these high standards. These standards were established by practicing radiologists and medical physicists who were experts in mammography. Facilities submitted quality control data, phantom images, dosimetry measurements and specific examples of their best clinical images for review by expert panels. The Mammography Accreditation Program became a model for five additional ACR imaging accreditation programs that have evolved since 1995 (Stereotactic Breast Biopsy, Breast Ultrasound, Ultrasound, Magnetic Resonance Imaging, and Nuclear Medicine). In order to successfully complete each of these programs, the facility must provide evidence of routine quality control as well as submit clinical images for review that meet the ACR standards for image quality. Requirements for personnel, phantom imaging and dose are modality-specific. The resultant image quality from many of these modalities are significantly dependent on consistent and appropriately-established film processing. Quality control of these processing systems is an integral part of these accreditation programs.
This chapter details the specific requirements for processing quality control recommended by these accreditation programs.
Chapter 4
Fundamentals of Silver Halide Film Design for Medical Imaging
Robert E. Dickerson - Health Imaging, Eastman Kodak Company
Silver halide based X-ray films have been the mainstay of radiography in the 20th century and will remain into the 21st century as they provide an efficient, high quality, cost effective solution to medical imaging. This chapter chronicles the evolution of X-ray films from their first uses to the present time. The very first X-ray images were coated on glass plates, exposed and processed in trays. The emulsions used in this process were non-specific morphology silver halide grains commonly described as three-dimensional (3-D) or pebble shaped grains. Such grains depended on their inherent spectral sensitivity of the silver halide grain used to match the light output of the first X-ray intensifying screens which were first made of calcium tungstate.
Later with the discovery of rare earth intensifying screens, silver halide grains were optically sensitized with sensitizing dyes to extend far beyond the inherent sensitivity of silver halide. This expanded the use of films from being just blue sensitive to orthochromatic sensitive and expanded the application of X-ray films for use with exposures by multiformat cameras and laser printers. Thus, the spectral sensitivity of silver halide films was extended from the blue region of the electromagnetic spectrum out into the infrared. In later years X-ray films utilized tabular or plate like grains that were very efficient in capturing the spectral emission of rare earth gadolinium oxysulfide intensifying screens.
Cubic grains were used in laser print films and recently in mammography films. Very small microcubic grains were used in radiation therapy films for oncology. Film coating structures have evolved also, starting with a single emulsion layer coated on glass plates and exposed with either a direct X-ray exposure or calcium tungstate intensifying screens. In the 1930's, film was first coated on flexible, transparent, polyestar supports and coated on both sides of the film This film was then exposed with a pair of intensifying screens which allowed for a significant increase in filin speed resulting in a decrease in X-ray exposure. This became the standard film format for many years until the introduction of Kodak InSight film in 1992.
InSight film was an asymmetric, zero crossover film that had different emulsions of different sensitivity and contrast on each side of the support. This film was exposed with intensifying screens that were also asymmetric in both speed and contrast. Such a system was tailored to meet the unique imaging requirements of thoracic radiography. Single emulsion films exposed with single intensifying screens remained exclusively in mammography which demanded the highest resolution possible. However, the introduction of Kodak MinR-L in 1999 demonstrated a unique coating format where an asymmetric, double coated film was exposed with a single intensifying screen. This film provided excellent contrast and resolution in imaging microcalcifications and breast tumors while also visualizing the whole breast.
A great deal of innovation in X-ray film / screen system occurred in the 20th century. Still, more ideas exist today for future film / screen systems that will improve the cost, convenience and image quality of medical imaging in the future.
Chapter 5
Design Basics and Component Functions Of Automatic Film Processors
Kenneth W. Oemcke
Eastman Kodak Company
Rochester, NY
There are many variables that influence radiographic image quality. One of the prime contributors is the x-ray film processor. The elements of the film processor need to be carefully designed to provide the optimal processing parameters. This chapter describes each of the processing steps, defines components in each step and describes the basic principles of processor design.
The four prime steps in film processing is reviewed: developing, fixing, washing, and drying. The most critical of these is the development step and must be given the most attention during the design phase. Development makes the latent image visible, therefore, extreme caution must be taken to assure that no artifacts are induced on the film. The fixing section removes unexposed, undeveloped silver crystals thereby making the image permanent. The washing section removes all chemicals from the film emulsion to assure long term stability of the image. And lastly, the drying section dries the film to allow immediate handling. In addition to these four sections there are many other factors to consider, such as, reliable transport, material selection and safety regulations. Options exist in processor, film, and chemical technology, which must also be considered during the design phase.
Chapter 6
Health, Safety and Environmental Progress in X-ray Film Processing
Richard Cataldi.
Health Imaging Division
Eastman Kodak Company
This chapter begins with a brief update regarding industry and regulatory trends affecting film processing since the 1992 Symposium. A variety of programs and products is presented as examples of the progress that has been made in understanding and reducing the impact of film processing on the environment and employee health and safety.
On the topic of "silver", an update is presented regarding joint efforts between industry and government aimed at studying the fate and effects of silver as well as education programs aimed at users of silver based films. Information regarding silver reclamation and film recycling is included.
Changes in the processing systems in the past 7 or 8 years are described. Progress in processing equipment is presented showing reduced usage of wash water and power. System approaches including both newer films and equipment demonstrate progress made in the reduction in the amount of processing chemicals needed to process a sheet of film. In addition to the amount of chemicals used, new processing chemical products are discussed that are formulated with materials generally considered of lesser impact to the environment and to the health and safety of employees.
Also mentioned are other support programs that are aimed at improving the overall health, safety and environmental impact of the processing system, along with a look at what may be coming to provide further progress in this area in the next 1 to 2 years.
Chapter 7
Film Processor Performance Audits and Common Problems
Gary T. Barnes, Ph. D.
UAB Medical Center
University of Alabama at Birmingham
Birmingham, AL
Processing is an important component of screen-film mammography. Subpar processing can result in a loss of film speed, decreased film contrast and artifacts all of which can compromise image quality and the diagnostic utility of the exam. Presented is a systematic approach to auditing processor performance. Checked are developer temperature, cycle time, processor developer and fixer specific gravities and pH replenishment tank developer and fixer specific gravities and pH sensitometric speed and contrast of the site's processor compared to a reference processor, hyporetention and dark room fog. Also evaluated are processor artifacts. These checks along with a review of the site's daily processor QC records provide insight into the site's processing. Discussed are findings of 25 consecutive processor audits and the problems identified. Of practical importance is that problems were found in more than 40% of the audits. Problems found included subpar film speed and contrast, specific gravities that are too high or too low, improper replenishment, improper chemistry mixing, rough rollers and processor wet pressure marks, squeegee roller malfunction, excessive hyporetention and excessive darkroom film fogging. It is of interest that hyporetention and darkroom fog problems were found even though these tests had been routinely done as part of the technologist QC program. Presented are example audit reports. It is concluded that processor performance should be audited on an annual basis by medical physicists in conjunction with the mammography equipment performance audit.
Chapter 8
Optimizing the Selection of Film and Film Processing in Screen-Film Imaging
R. Edward Hendrick, Ph.D. and Eric Berns, M.S.
Lynn Sage Comprehensive Breast Center
Northwestern University Medical School
Chicago, IL
The purpose of this chapter is to describe methods that allow clinical sites to optimize their selection of film and film processing conditions for mammography. The methods are fully applicable to other modalities that use film-screen imaging.
These methods rely on collection of 21-step sensitometry data using the site's clinical film and processing conditions, as normally done for quality control. The methods require construction of a gamma plot for each sensitometric strip. The gamma plot displays the film-processing contrast at each optical density from minimum (base plus fog) to maximum (Dma,) . Gamma plots provide a fingerprint of film and processing conditions at the time of acquisition of the sensitometric strip. Methods to compare the contrast available in different films and with different processing conditions are described.
Between December 1989 and October 1999, 216 on-site physics surveys were conducted at approximately 30 mammography facilities participating in the Colorado Mammography Advocacy Project(CMAP). Twenty-five site surveys were conducted in 1999. To assess film and processing at each site, sensitometric strips were obtained with the site's clinical film and processor, using the same sensitometer and densitometer for each site. Gamma plots were obtained for each site's film and processing. The integrated area under the gamma plot curve (Ag) was used as a single parameter to represent film-processing contrast. These results provide a historical picture of the film-processing contrast that existed mammograms over the last decade. Ag values averaged across all sites by year increased by 70% between 1989 and 1999, from a 1989 average of 7.5 to a 1999 average of 12.9. Maximum optical densities in mammograms increased by 27% over the same time period, from a 1989 average of 3.6 to a 1999 average of 4.52.
The 25 sites surveyed in 1999 provide a clear picture of the range of film-processing contrast at mammography sites in the U.S. Ag values ranged by nearly a factor of two, from 8.6 to 16.8 (mean: 12.9): Dmax values ranged by 26%, from 3.82 to 4.80 (mean 4.38).
These results indicate that there has been significant improvement in the average contrast in mammograms over the last decade. These results indicate that there is still room for improvement, since there was nearly a 2-fold range in film-processing contrast among the 25 clinical mammography sites surveyed in 1999.
Chapter 9
Sources and Control of Variability in Dry Laser Imagers
Eric Donaldson
Eastman Kodak Company
Oakdale, MN
This chapter gives an overview of Dry Laser Imager equipment technology and the sources of image variability that can occur in these systems. Special attention is given to the photothermographic processing systems that are available and the critical performance variables in each. The analogies of thermal processing to wet film processing are discussed, as well as the methods used to maintain image quality. A practical view of trouble shooting is also provided.
Chapter 10
Dry Media Imaging Technology
Neil J. Anderson
Eastman Kodak Company
Oakdale, MN.
In the mid-1990's, a new paradigm was introduced to medical imaging departments that has created a revolutionary change in workflow, department planning and cost structure. "Dry imaging" has, in a very short time, become the preferred technology for producing hardcopy in the digital imaging arena.
This chapter describes the different dry film technologies currently used in medical diagnostic imaging - specifically in transmission radiographs. Since the introduction of the first "dry"imaging systems in the early '90's, every major film manufacturer has introduced at least one dry solution to the marketplace. The technologies have not all been the same, but each brings about many of the inherent advantages in dry imaging - elimination of wet chemistry, siting flexibility, reduced space requirements, reduced environmental impact, and usually a reduction in overall operating costs.
Each major dry technology is explained, focusing on mechanisms for transferring image information to the media and processing the media to produce the image. Sources of variability in different media technologies is also discussed.
Chapter 11
The Role of the Dealer in Film Processing
A. L. Hawkins
Marconi Medical Systems, Inc.
Indianapolis, IN.
This chapter explores the evolution of the dealer organization over the last 20 years and how the dealer network has been impacted by the following:
Industry consolidation - providers, payers, manufacturers and dealers
Cost reduction pressures
Reimbursal reductions to the customer base
Technology advancement
Stricter regulatory controls
Training and certification requirements
Environmental concerns
There is also a discussion of how the customer has changed and what today's customer expects/requires of the modern dealer, such as:
Processing objectives consultation
Darkroom design / Architectural support
Processing equipment specifications
Facilities support
Equipment order consultation
Processing chemistry specifications
Equipment installation
Establish QC / QA parameters
Exposure optimization support
Equipment Maintenance
Quality Assurance support / consultation
Continuing technology consultation
Finally, the chapter looks at the future of the customer dealer relationship with regard to industry trends. PACS, dry laser printing and print media, reduction in chemical utilization all will have an effect on the future of the dealer.
Chapter 12
The Role of the Technologist in Film Processing Quality Control and Troubleshooting
Susan M. Jaskulski, R.T.(R)(M)
Marconi Medical Systems, Inc.
Cleveland, OH
Technologists play a critical role in all film processing quality control (QC) tests and procedures, especially in mammography, which is regulated nationally in the United States.
In order to efficiently perform film processing QC and to minimize time spent in troubleshooting, technologists should be well-informed about proper processor set-up, operation and all other aspects of the processing environment. Close communication between the technologist and the processor service engineer is not required but makes good sense in order to establish and maintain a viable QC program. All technologists, but especially those technologists responsible for QC, should ensure that the processor, film, and chemical manufacturers' recommendations, developed to help facilities optimize image quality, have been followed regarding:
Processor installation.
Safelighting.
Processor and darkroom ventilation.
Environmental temperature and relative humidity.
Processor maintenance.
Cycle time.
Fresh processing chemicals, properly mixed, including the specified amount of the chemical manufacturer's developer starter.
Developer and fixer replenishment rates, based on the volume and type(s) of film.
Solution and dryer temperatures.
This chapter highlights those areas where closer adherence to the manufacturers' recommendations may further improve clinical image quality.
When test results indicate the need for troubleshooting, most technologists call upon outside resources for assistance, i.e., processor service engineers, film company representatives and/or the medical physicist, since technologists do not generally receive extensive training in this area. Consideration of the following topics may assist technologists in taking their quality control program to the next higher level:
Using the phantom image as a troubleshooting tool.
Using more than five days to establish the processor QC chart.
Minimizing chemical oxidation.
Calculating toe, mid and average gradients.
Using H&:D and contrast/optical density curves as a troubleshooting tool.
Chapter 13
The Role of the Medical Physicist in Film Processing -
Mammography Accreditation and Certification
Robert J. Pizzutiello, Jr.
Upstate Medical Physics
Victor, NY
The role of the medical physicist as a consultant is perhaps never more important than when suboptimal film processing threatens the quality of a mammographic image. The steep contrast of mammography film coupled with the FDA regulations and ACR recommendations in this regard create a potential for apparent problems to occur with some regularity. The medical physicist's role regarding the film processor Mammography Equipment Evaluation (MEE), processor QC and phantom imaging is addressed.
Chapter 14
Film Processor Darkroom Design Considerations
Stephen J. Pflanz and Kurt M. Cleland
Eastman Kodak Company
Rochester, NY.
This chapter reviews requirement assessment, evaluating the existing site, defining site redesign needs, obtaining equipment installation instructions and site specification documentation, developing a plan and reviewing plans with an architect.
Processor Installation:
Covers recommended service clearances, dryer exhaust, room ventilation and air exchanges, film storage, film handling, chemical storage, replenishment lines, cleanliness of area and service requirements
Careful planning is essential in designing a new darkroom or processing area or in redesigning an existing area. Spending time early in the design process will more than pay off in the end with a functional, well planned work space.
The first decisions that need to be made are the desired location of the processing area and how much space is required. Another major decision is wether or not a darkroom is required, or if a roomlight processing area is more appropriate.
Once these decisions have been made, consideration can be given to what equipment will be installed in the area Of course, this plays a large role in determining the actual amount of space that is required. After specific information on the equipment specifications has been obtained from the equipment manufacturers, more detailed plans for the processing area can be made. These plans include designing the floor plan or layout of the area. It is important to work with an architect to develop detailed drawings and to determine the renovations or construction that will be required. In designing the layout of the area, consideration should be given to the functions to be performed in the area and to optimal work flow.
Once the layout has been completed, plans need to be made for providing the utilities required for the equipment. It is important to use existing plumbing, drams, power, etc., whenever possible, in order to minimize costs. Other considerations are the placement of replenisher tanks, film bins and other required items.
This planning process may seem time-consuming, but it is critical for ensuring that the new processing area will be well-designed and offer an efficient, functional work space. It is important to begin the planning early in the design process to avoid costly problems further along in the renovations or construction.